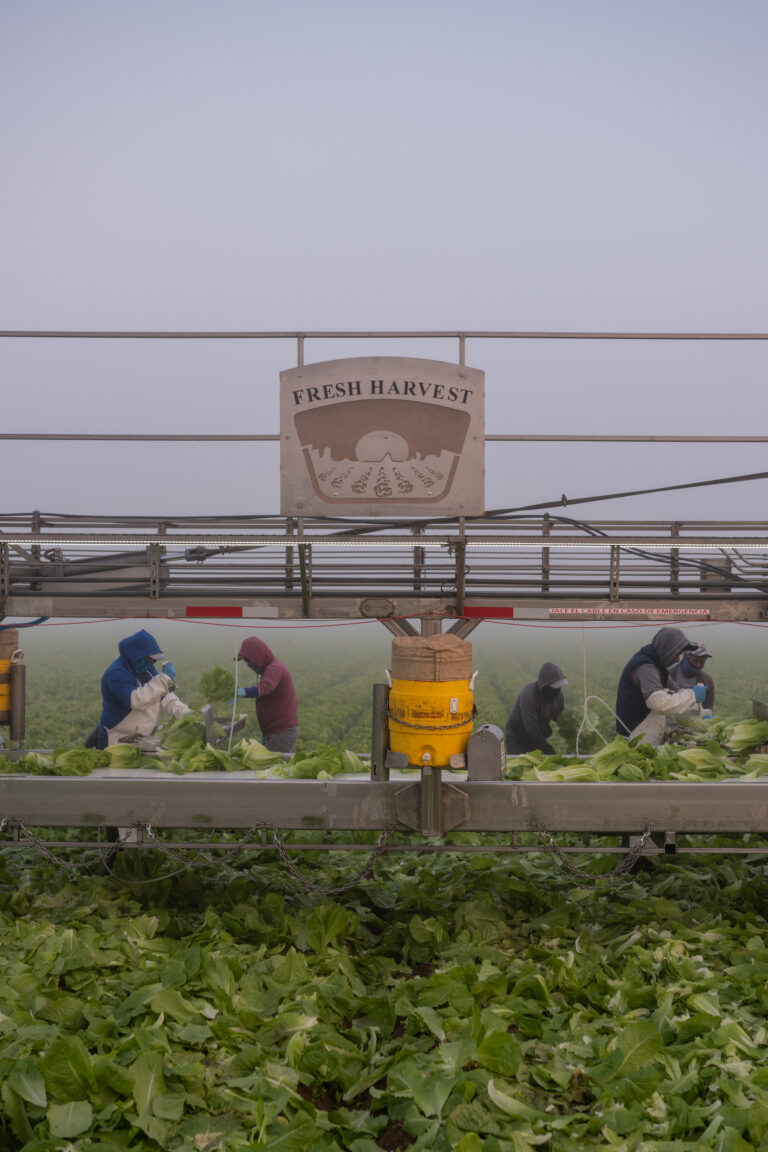
▲ This 100-foot-wide harvester is able to make 180-degree turns in the field and travel between jobs
When an increase in immigration law enforcement at the U.S.-Mexico border in 2006 created a sudden and severe labor shortage, Steve Scaroni found himself at a crossroads.
Steve and his sons own and operate Scaroni Family of Companies, a full-service turnkey harvest business near El Centro, California. Without labor, he was dead in the water.
“We lost about 40% of our workforce in 40 hours” said Scaroni, who, with his sons Matt and David, provides supervision, equipment and labor to growers in California, Arizona, Nevada, Colorado, Texas and Florida.
There was nothing we could do to meet our contractual obligations
Scaroni began exploring the U.S. Department of Labor’s H-2A temporary agricultural program. But it required some creativity. At the time, the program had only been used on the East Coast; with vaguely written regulations and no other West Coast participants, even the program administrators were unsure how to implement it here.
Steve spent the next four years working side-by-side with the Department of Labor ironing out the details of how H-2A should operate. Like any process requiring consensus, it required creativity, compromise and trial
and error.
We went from a somewhat combative relationship to a more collaborative one, working together toward a mutual understanding of how the program should work, Steve said. We led that charge.
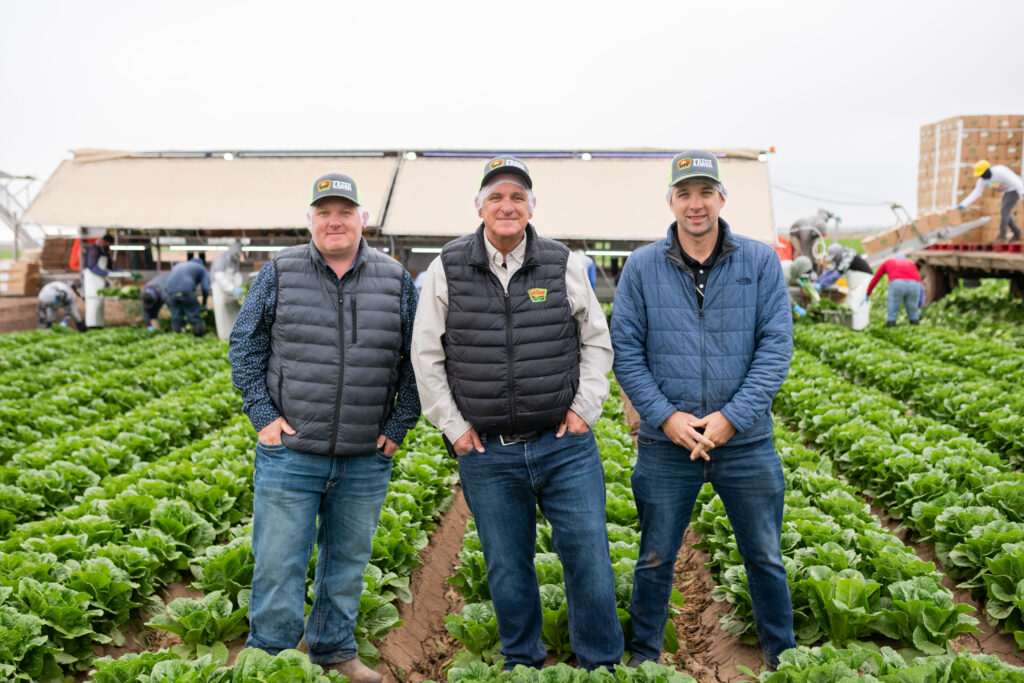
▲ Steve Scaroni, center, along with his sons Matt, left, and David, right, have made innovating for efficiency a business practice.
Today, the family has 6,000 people on payroll and employs up to 3,500 at any given time. Their company is one of the largest West Coast participants of H-2A. The family has gone even further, establishing a leadership program at their farming operation in northern Baja, Mexico, and among their USA H-2A workforce, in which employees who show promise are given training in management and other skills.
With opportunities in crew supervision, mechanics, truck driving, accounting, and back office, workers can better their lives while filling critical mid-level management roles for the Scaroni family.
“When you train someone who came from nothing and give them the opportunity to advance, the loyalty is unbelievable,” Steve said. “That’s been a tremendous help.”
On another front, when labor shortages at salad plants made it nearly impossible to continue coring lettuce at the plant level, Steve co-created a new method of harvesting lettuce in the field that is now used across the industry. Workers use a double-bladed knife they patented to first cut the plant from the ground, then core it. Next, a preserving liquid created by Fresh Express is sprayed directly into the core cavity, creating ready-to consume lettuce, wherever it is shipped.
Beyond perfecting his labor supply chain, Steve and his sons have boosted efficiencies by refining their harvest equipment and techniques.
For example, the 100-foot-wide machine, which harvests iceberg and romaine lettuce, must be able to turn 180 degrees in the field for each pass. The Scaronis perfected a telescoping design, allowing the machine to accordion into itself and contract down to 50 feet. This also makes it possible to transport the large machine. When asked what drives him to continually innovate for efficiency and quality, Steve points back to his roots as a grower and his mission to serve his customers.
“We were farmers first, and we really understand the crop investment,” he said. “We’re about making sure that investment is recouped for a profit by our customers. We have the farmer blood in our veins.” ◆
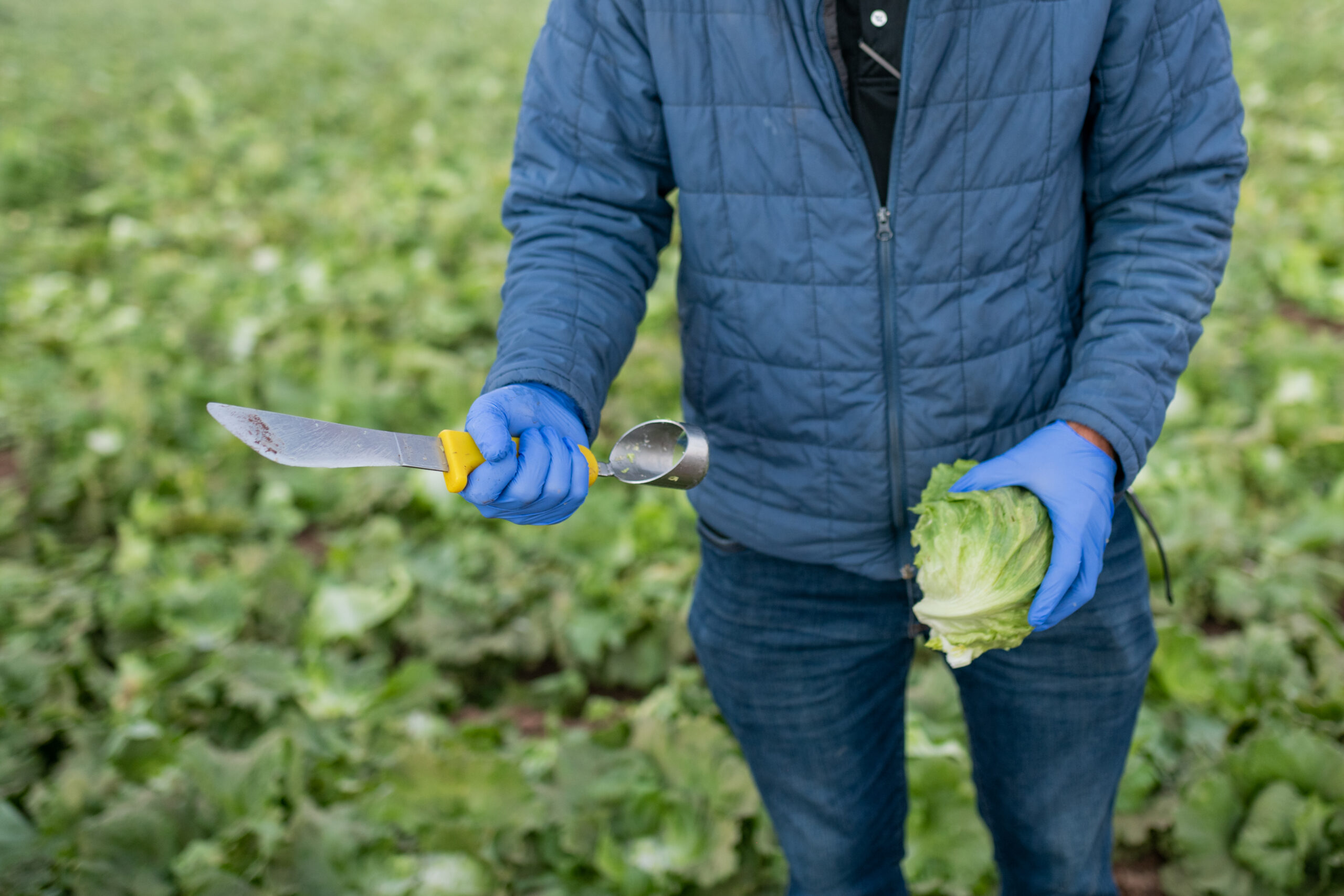
▲ Among Steve Scaroni’s many innovations is this knife, which allows workers to core lettuce efficiently in the field.